CAN (Controller Area Network)
CAN (Controller Area Network)
Controller Area Network (CAN) is a robust and efficient communication protocol designed primarily for automotive and industrial applications. It facilitates reliable data exchange between electronic control units (ECUs) and other devices, ensuring seamless operation and integration. This article explores the origins, architecture, applications, and future of CAN bus technology.
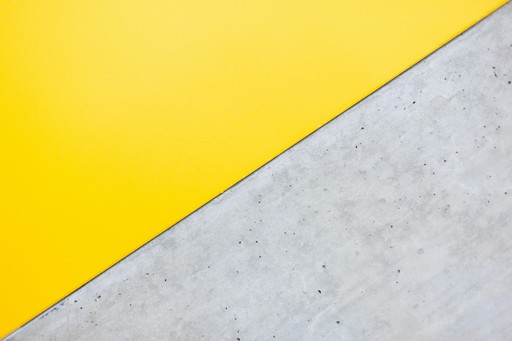
Controller Area Network (CAN) is a robust and efficient communication protocol designed primarily for automotive and industrial applications. It facilitates reliable data exchange between electronic control units (ECUs) and other devices, ensuring seamless operation and integration. This article explores the origins, architecture, applications, and future of CAN bus technology.
Origins and Development
The development of the CAN bus began in 1983 at Robert Bosch GmbH, with the official release of the protocol in 1986 at the Society of Automotive Engineers (SAE) congress in Detroit, Michigan. The first CAN controller chips were introduced by Intel and Philips in 1987, marking a significant milestone in automotive communication technology. The Mercedes-Benz W140, released in 1991, was the first production vehicle to feature a CAN-based multiplex wiring system, showcasing the protocol's potential for reducing wiring complexity and enhancing communication efficiency.
Architecture and Principles
CAN bus operates on a multi-master serial bus standard, allowing multiple nodes (ECUs or other devices) to communicate over a two-wire differential bus. The protocol uses a message-based, half-duplex communication method, where each message contains an identifier (ID) that determines its priority. The CAN bus employs a lossless bitwise arbitration method to resolve contention, ensuring that the highest priority message is transmitted without delay. This is achieved through dominant and recessive bits, where dominant bits (logical 0) override recessive bits (logical 1) during arbitration.
The physical organization of the CAN bus involves a twisted pair of wires with a characteristic impedance of 120 Ω, terminated at each end with a resistor. The differential signaling used in CAN bus enhances noise immunity, making it suitable for electrically noisy environments. The bus operates at various bit rates, with high-speed CAN supporting up to 1 Mbit/s and low-speed (fault-tolerant) CAN supporting up to 125 kbit/s.
Versions and Enhancements
Classical CAN (CAN 2.0)
CAN 2.0A (Standard CAN) and CAN 2.0B (Extended CAN) are the most widely used versions, with CAN 2.0A using an 11-bit identifier and CAN 2.0B using a 29-bit identifier. The extended identifier in CAN 2.0B allows for a greater number of unique message identifiers, beneficial in complex systems with many nodes. However, this increase in unique identifiers also increases frame length, potentially reducing the maximum data rate.
CAN FD (Flexible Data-Rate)
Introduced by Bosch in 2012, CAN FD addresses the need for higher data transfer rates in modern vehicles. It allows for variable data rates during the transmission of a single frame, with the arbitration phase occurring at a lower data rate and the data payload transmitted at a higher rate. CAN FD also introduces a flexible data field size, increasing the maximum size from 8 bytes to 64 bytes. This enhancement enables more efficient data transmission, particularly for high-resolution sensor data or software updates. CAN FD maintains backward compatibility with CAN 2.0 devices, allowing coexistence on the same bus.
CAN XL
CAN XL, specified by CiA 610-1, supports up to 2,048-byte payloads and data rates up to 20 Mbit/s. It bridges the gap between CAN FD and Ethernet (100BASE-T1) while maintaining CAN's collision-resolution benefits. CAN XL controllers can also handle Classical CAN and CAN FD communication, ensuring compatibility in mixed networks. Its large data fields allow for higher layer protocols like IP (Internet Protocol) and the tunneling of Ethernet frames.
Applications and Industry Adoption
The CAN bus protocol has found widespread application in various industries due to its reliability, efficiency, and flexibility.
Automotive Industry
Modern automobiles rely heavily on CAN bus for communication between ECUs, enabling advanced features such as auto start/stop, electric park brakes, parking assist systems, and collision avoidance systems. The protocol's ability to prioritize messages ensures that critical functions are not compromised, enhancing safety and performance.
Industrial Automation
CAN bus is used in industrial settings for communication between sensors, actuators, and control devices. Its robustness and real-time capabilities make it ideal for applications requiring precise control and monitoring.
Other Applications
The CAN bus protocol is also employed in agricultural equipment, aviation electronics, electric generators, building automation, medical instruments, and maritime applications. Its versatility and reliability make it a preferred choice for various control and communication tasks.
Future Trends and Innovations
As technology advances, the CAN bus protocol continues to evolve to meet the demands of modern applications. The introduction of CAN FD and CAN XL has significantly enhanced data transfer rates and payload sizes, enabling more complex and data-intensive applications. The protocol's ability to coexist with other communication standards, such as Ethernet, ensures its relevance in the era of connected devices and the Internet of Things (IoT).
Conclusion
Controller Area Network (CAN) bus technology has revolutionized communication in automotive and industrial applications. Its robust architecture, efficient data transmission, and real-time capabilities make it an essential component in modern control systems. As the protocol continues to evolve, its applications and benefits are expected to expand, driving innovation and efficiency across various industries.