OPC (OLE for Process Control)
OPC (OLE for Process Control)
OPC (OLE for Process Control) is a widely-used communication standard designed to facilitate seamless data exchange and interoperability between various devices and systems in industrial automation. Originally developed in 1996, OPC has evolved to become a cornerstone in the integration of process control, manufacturing automation, and other industrial applications.
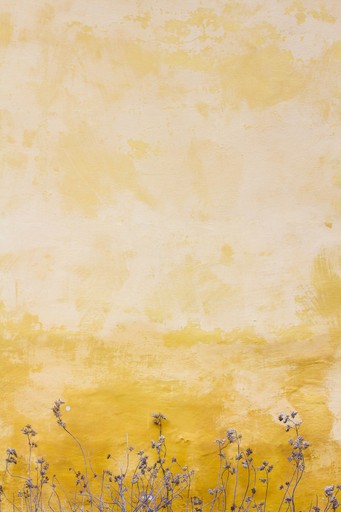
OPC (OLE for Process Control) is a robust and widely-used communication standard designed to facilitate seamless data exchange and interoperability between various devices and systems in industrial automation. Originally developed in 1996, OPC has evolved to become a cornerstone in the integration of process control, manufacturing automation, and other industrial applications.
Key Terms
OPC Specification: A set of standards and specifications that define a common interface for communication between industrial automation systems and devices.
OPC Server: A software program that converts hardware communication protocols into the OPC protocol, allowing OPC clients to access data from process control devices.
OPC Client: An application that communicates with OPC servers to access real-time data, historical data, and alarms and events.
OPC Data Access (DA): The most common OPC specification, used for reading and writing real-time data from process control devices.
OPC Historical Data Access (HDA): A specification that allows access and retrieval of archived data from process control devices.
OPC Alarms and Events (A&E): A specification that defines the exchange of alarm and event type messages, as well as variable states and state management.
OPC Unified Architecture (UA): A platform-independent specification that combines the functionality of existing OPC interfaces with new technologies such as XML and Web services.
How OPC Works
Imagine an industrial facility with various process control devices, such as programmable logic controllers (PLCs) and distributed control systems (DCS). OPC enables these devices to communicate seamlessly with each other and with higher-level systems, such as human-machine interfaces (HMIs) and supervisory control and data acquisition (SCADA) systems. Here's how it works:
Data Exchange: OPC servers convert the proprietary communication protocols of process control devices into the OPC protocol. OPC clients can then access this data in a standardized format, regardless of the underlying hardware.
Interoperability: OPC ensures that devices from different manufacturers can work together seamlessly. This is achieved through standardized objects, interfaces, and methods defined in the OPC specification.
Real-Time Data Access: OPC Data Access (DA) allows OPC clients to read and write real-time data from process control devices. This enables operators to monitor and control industrial processes in real-time.
Historical Data Access: OPC Historical Data Access (HDA) allows OPC clients to access and retrieve archived data from process control devices. This is essential for trend analysis, reporting, and compliance.
Alarms and Events: OPC Alarms and Events (A&E) allows OPC clients to receive and manage alarms and events from process control devices. This enables operators to respond to critical situations promptly.
Platform Independence: OPC Unified Architecture (UA) extends the capabilities of OPC to non-Windows platforms, making it a truly platform-independent solution.
Components of OPC
OPC Specification: A set of standards and specifications that define a common interface for communication between industrial automation systems and devices.
OPC Server: A software program that converts hardware communication protocols into the OPC protocol, allowing OPC clients to access data from process control devices.
OPC Client: An application that communicates with OPC servers to access real-time data, historical data, and alarms and events.
OPC Data Access (DA): The most common OPC specification, used for reading and writing real-time data from process control devices.
OPC Historical Data Access (HDA): A specification that allows access and retrieval of archived data from process control devices.
OPC Alarms and Events (A&E): A specification that defines the exchange of alarm and event type messages, as well as variable states and state management.
OPC Unified Architecture (UA): A platform-independent specification that combines the functionality of existing OPC interfaces with new technologies such as XML and Web services.
Importance of OPC
OPC is crucial for ensuring efficient and reliable communication in industrial automation systems. It provides a standardized method for devices to communicate, making it easier to integrate and manage different systems within an industrial facility. OPC is widely used in various applications, including:
Process Control: OPC is used to monitor and control industrial processes, such as manufacturing, chemical, and oil and gas.
Building Automation: OPC is used to manage and control building systems, such as HVAC, lighting, and security.
Discrete Manufacturing: OPC is used to monitor and control discrete manufacturing processes, such as assembly lines and robotics.
Energy Management: OPC is used to monitor and control energy consumption in industrial facilities, helping to reduce costs and improve efficiency.
Real-World Examples
Industrial Automation: OPC is used to integrate various process control devices, such as PLCs and DCS, with higher-level systems, such as HMIs and SCADA systems.
Building Automation: OPC is used to integrate building systems, such as HVAC and lighting, with energy management systems.
Manufacturing: OPC is used to monitor and control manufacturing processes, such as assembly lines and robotics, in real-time.
Implementing OPC
Understand OPC Fundamentals: Learn the basic principles of OPC, including its specifications, interfaces, and methods.
Network Configuration: Set up your OPC network by configuring OPC servers and clients with appropriate addresses and ensuring proper wiring for the chosen network technology.
Software Tools: Utilize OPC software tools to configure and monitor OPC servers and clients. These tools can help you set parameters, test communication, and diagnose issues.
Optimization: Fine-tune OPC settings, such as data access methods and communication protocols, to optimize performance for your specific application. Consider factors like network latency and data throughput.
Integration: Integrate OPC with other systems, such as HMIs and SCADA systems, to create a cohesive automation solution. Ensure compatibility and seamless data exchange between different protocols and devices.
Challenges and Considerations
Network Management: Managing an OPC network can be complex, especially in large industrial facilities with many devices. Ensuring reliable communication and troubleshooting issues can be challenging.
Interoperability: While OPC is designed to be interoperable, differences in implementation between manufacturers can sometimes cause compatibility issues.
Security Measures: OPC was not originally designed with security in mind, making it vulnerable to cyber threats. Implementing additional security measures, such as encryption and access controls, is crucial.
Maintenance Requirements: Regular maintenance and upgrades are necessary to keep the OPC network running smoothly. This includes updating software, replacing faulty devices, and monitoring network performance.
Platform Independence: Ensuring that OPC solutions are platform-independent and can operate on various hardware and software platforms is essential for modern industrial automation systems.