Profinet
Profinet
PROFINET is a robust and versatile industrial communication standard that plays a vital role in industrial automation networks. Its standardized approach ensures reliable and efficient communication between devices, making it a popular choice for various applications in the manufacturing and process industries.
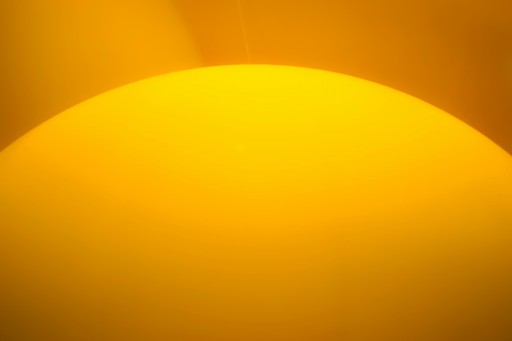
PROFINET is a robust and widely-used industrial communication standard designed to facilitate seamless data exchange and interoperability between various devices and systems in automation networks. Developed by PROFIBUS & PROFINET International (PI), PROFINET has become a cornerstone in the integration of industrial automation, process control, and other related applications.
Key Terms
PROFINET: An industrial Ethernet standard that enables real-time communication between automation systems and devices.
PROFINET Devices: Components such as controllers, I/O devices, and drives that communicate using the PROFINET protocol.
Real-Time Communication: The ability to exchange data with minimal latency, ensuring timely and accurate control of industrial processes.
Industrial Ethernet: A network protocol that uses Ethernet technology to connect industrial devices, providing high-speed and reliable communication.
Interoperability: The ability of different devices and systems to communicate and work together seamlessly.
PROFINET IO: A component of PROFINET that focuses on data exchange between controllers and field devices.
PROFINET CBA: A component of PROFINET that enables communication between multiple controllers in a distributed automation system.
How PROFINET Works
PROFINET leverages the power of Ethernet to provide high-speed and reliable communication between industrial devices. Here's how it works:
Network Architecture: PROFINET uses a standard Ethernet backbone to connect various devices, such as controllers, I/O devices, and drives. This architecture ensures high-speed data transfer and robust communication.
Real-Time Communication: PROFINET supports real-time communication, which is crucial for industrial automation. It ensures that data is exchanged with minimal latency, enabling precise control of industrial processes.
Interoperability: PROFINET ensures that devices from different manufacturers can communicate seamlessly. This is achieved through standardized protocols and data models defined in the PROFINET specification.
Scalability: PROFINET networks can be easily scaled to accommodate additional devices and systems. This makes it suitable for both small and large industrial automation networks.
Security: PROFINET includes provisions for cybersecurity, ensuring that communication between devices is secure and protected against threats.
Components of PROFINET
PROFINET: An industrial Ethernet standard that enables real-time communication between automation systems and devices.
PROFINET Devices: Components such as controllers, I/O devices, and drives that communicate using the PROFINET protocol.
Real-Time Communication: The ability to exchange data with minimal latency, ensuring timely and accurate control of industrial processes.
Industrial Ethernet: A network protocol that uses Ethernet technology to connect industrial devices, providing high-speed and reliable communication.
Interoperability: The ability of different devices and systems to communicate and work together seamlessly.
PROFINET IO: A component of PROFINET that focuses on data exchange between controllers and field devices.
PROFINET CBA: A component of PROFINET that enables communication between multiple controllers in a distributed automation system.
Importance of PROFINET
PROFINET is crucial for ensuring reliable and efficient communication within industrial automation networks. It provides a standardized framework that enhances interoperability, reduces integration costs, and improves overall system performance. The standard is widely used in various applications, including:
Manufacturing Automation: PROFINET is used to control and monitor manufacturing processes, ensuring precise and efficient operation.
Process Automation: PROFINET is used in process industries, such as chemical and pharmaceutical, to monitor and control production processes.
Building Automation: PROFINET is used to manage and control building systems, such as HVAC, lighting, and security.
Renewable Energy Integration: PROFINET supports the integration of renewable energy sources, such as solar and wind, into the power grid.
Real-World Examples
Automotive Manufacturing: PROFINET is used to integrate various automation systems in automotive manufacturing plants, ensuring seamless communication and efficient operation.
Chemical Processing: PROFINET is used to monitor and control chemical processing plants, enhancing safety and efficiency.
Building Management: PROFINET is used to integrate building systems, such as HVAC and lighting, with energy management systems.
Implementing PROFINET
Phase 1: Planning and Assessment
Assess Needs: Evaluate the specific requirements of your industrial automation network. Identify the goals and objectives you aim to achieve with PROFINET implementation.
Stakeholder Engagement: Engage with stakeholders, including engineers, operators, and IT personnel, to ensure alignment and support for the project.
Feasibility Study: Conduct a feasibility study to determine the technical and economic viability of implementing PROFINET in your existing infrastructure.
Phase 2: Design and Configuration
Network Architecture: Design the architecture of your PROFINET network, ensuring compliance with the standard's requirements. Define the communication protocols, data models, and network topology.
Device Selection: Choose PROFINET-compliant devices that meet the required functionalities and performance criteria. Ensure that the selected devices are interoperable.
Configuration: Configure the PROFINET network using standardized tools and protocols. Define the data exchange mechanisms, communication settings, and device configurations.
Phase 3: Implementation and Testing
Installation: Install the selected PROFINET devices in the industrial environment. Ensure proper wiring and connectivity as per the designed architecture.
Integration: Integrate the devices into the PROFINET network. Configure the communication protocols and data exchange mechanisms according to PROFINET standards.
Testing: Conduct thorough testing to ensure that the system complies with PROFINET and performs as expected. Validate the configuration and communication between devices.
Phase 4: Training and Documentation
Training: Provide comprehensive training for personnel involved in the operation and maintenance of the PROFINET-based system. Ensure that they understand the standard's requirements and best practices.
Documentation: Maintain detailed documentation of the system design, configuration, and testing results. This documentation will be crucial for future maintenance and troubleshooting.
Challenges and Considerations
Technical Challenges
Complexity: Implementing PROFINET can be complex, requiring a deep understanding of the standard and its components. Ensuring that all devices and systems are correctly configured and integrated is crucial.
Interoperability Issues: While PROFINET aims to ensure interoperability, differences in implementation between manufacturers can sometimes cause compatibility issues. Thorough testing and validation are necessary to identify and resolve these issues.
Legacy Systems: Integrating PROFINET with existing legacy systems can be challenging. Ensuring seamless communication and data exchange between old and new systems requires careful planning and configuration.
Operational Considerations
Cybersecurity: Ensuring the security of communication between devices is crucial. Implementing robust cybersecurity measures is essential to protect against threats. Regular security audits and updates are necessary to maintain a secure environment.
Maintenance: Regular maintenance and updates are necessary to keep the system running smoothly and ensure compliance with the latest standards. This includes updating software, replacing faulty devices, and monitoring network performance.
Scalability: Ensuring that the system can scale to accommodate future expansions and upgrades is important for long-term sustainability. The system should be designed with scalability in mind to easily integrate new devices and functionalities.
Organizational Factors
Training: Providing adequate training for personnel is essential to ensure proper implementation and operation of PROFINET-based systems. Ongoing training and support are necessary to keep up with technological advancements and best practices.
Vendor Support: Working with vendors that provide comprehensive support for PROFINET-compliant devices is crucial for successful implementation and troubleshooting. Ensuring that vendors offer timely support and updates is important.
Compliance: Regular audits and compliance checks are necessary to ensure that the system adheres to the latest PROFINET standards and regulations. Maintaining compliance helps in avoiding potential issues and ensures the system's reliability and performance.
Future-Proofing
Technology Advancements: Staying updated with the latest advancements in PROFINET technology is essential. Regularly reviewing and integrating new features and improvements can enhance the system's performance and capabilities.
Industry Standards: Keeping up with industry standards and best practices ensures that the PROFINET implementation remains relevant and effective. Participating in industry forums and workshops can provide valuable insights and updates.
Sustainability: Implementing sustainable practices in the design and operation of the PROFINET network can reduce environmental impact and improve long-term efficiency.
PROFINET is a robust and versatile industrial communication standard that plays a vital role in industrial automation networks. Its standardized approach ensures reliable and efficient communication between devices, making it a popular choice for various applications in the manufacturing and process industries.