Modbus TCP
Modbus TCP
Modbus TCP is based on the Modbus protocol, which was originally developed in 1979 by Modicon (now part of Schneider Electric) for serial communication. By utilizing TCP/IP, Modbus TCP enables high-speed and scalable communication, making it ideal for modern industrial automation systems.
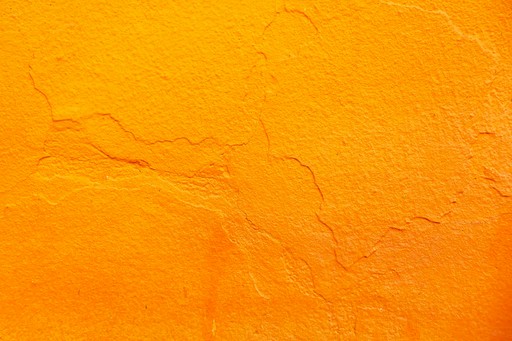
Modbus TCP is based on the Modbus protocol, which was originally developed in 1979 by Modicon (now part of Schneider Electric) for serial communication. By utilizing TCP/IP, Modbus TCP enables high-speed and scalable communication, making it ideal for modern industrial automation systems.
Unlike Modbus RTU, which operates over serial connections (RS-232/RS-485), Modbus TCP uses Ethernet networks, allowing multiple devices to communicate without complex wiring. It is widely used for industrial automation, energy management, and SCADA (Supervisory Control and Data Acquisition) systems.
How Modbus TCP Works
Client-Server Model: Modbus TCP follows a client-server architecture where a client (e.g., an HMI or SCADA system) requests data from or sends commands to a server (e.g., a PLC or sensor).
TCP/IP Transmission: Messages are encapsulated within TCP/IP packets, ensuring reliable communication over Ethernet.
Function Codes: Like traditional Modbus, Modbus TCP uses function codes to read, write, or control device registers.
No Checksum Required: Unlike Modbus RTU, which includes a checksum for error detection, Modbus TCP relies on the built-in error-checking mechanisms of TCP/IP.
Key Features
Ethernet-Based Communication: Utilizes standard Ethernet, allowing easy integration with IT and OT networks.
Scalability: Supports multiple devices without requiring point-to-point wiring, simplifying network expansion.
Interoperability: Compatible with a wide range of industrial devices from different manufacturers.
Reliability: Uses TCP/IP for error detection and packet retransmission, ensuring stable communication.
Ease of Configuration: Simplifies setup compared to serial-based Modbus RTU, with automatic addressing via IP networks.
Common Applications
🔹 Industrial Automation: Connecting PLCs, HMIs, and sensors for real-time monitoring and control.
🔹 SCADA Systems: Enabling remote control and data acquisition from industrial equipment.
🔹 Energy Management: Monitoring power meters, circuit breakers, and renewable energy systems.
🔹 Building Automation: Controlling HVAC, lighting, and access control systems.
Comparison: Modbus TCP vs. Modbus RTU
Feature | Modbus TCP | Modbus RTU |
---|---|---|
Transport Medium | Ethernet (TCP/IP) | Serial (RS-232/RS-485) |
Architecture | Client-Server | Master-Slave |
Speed | High (up to 1 Gbps) | Lower (115.2 kbps max) |
Wiring Complexity | Low | High |
Error Checking | Handled by TCP/IP | CRC Checksum |
Network Size | Scalable with IP addressing | Limited to 32 devices per RS-485 bus |
Conclusion
Modbus TCP is a robust and widely adopted protocol for industrial automation, providing a reliable and scalable solution for device communication over Ethernet. Its compatibility with existing Modbus systems, ease of integration, and strong network reliability make it a preferred choice for industries transitioning to modern automation and IoT-based infrastructures.